Specifications
Table Of Contents
- Rosemount 3051S Series Scalable Pressure, Flow, and Level Solution with HART® Protocol
- Title Page
- Table of Contents
- Section 1 Introduction
- Section 2 Installation
- Section 3 Configuration
- Section 4 Operation and Maintenance
- Section 5 Troubleshooting
- Section 6 Safety Instrumented Systems
- Section 7 Advanced HART Diagnostic Suite
- Appendix A Specifications and Reference Data
- Appendix B Product Certifications
- Index
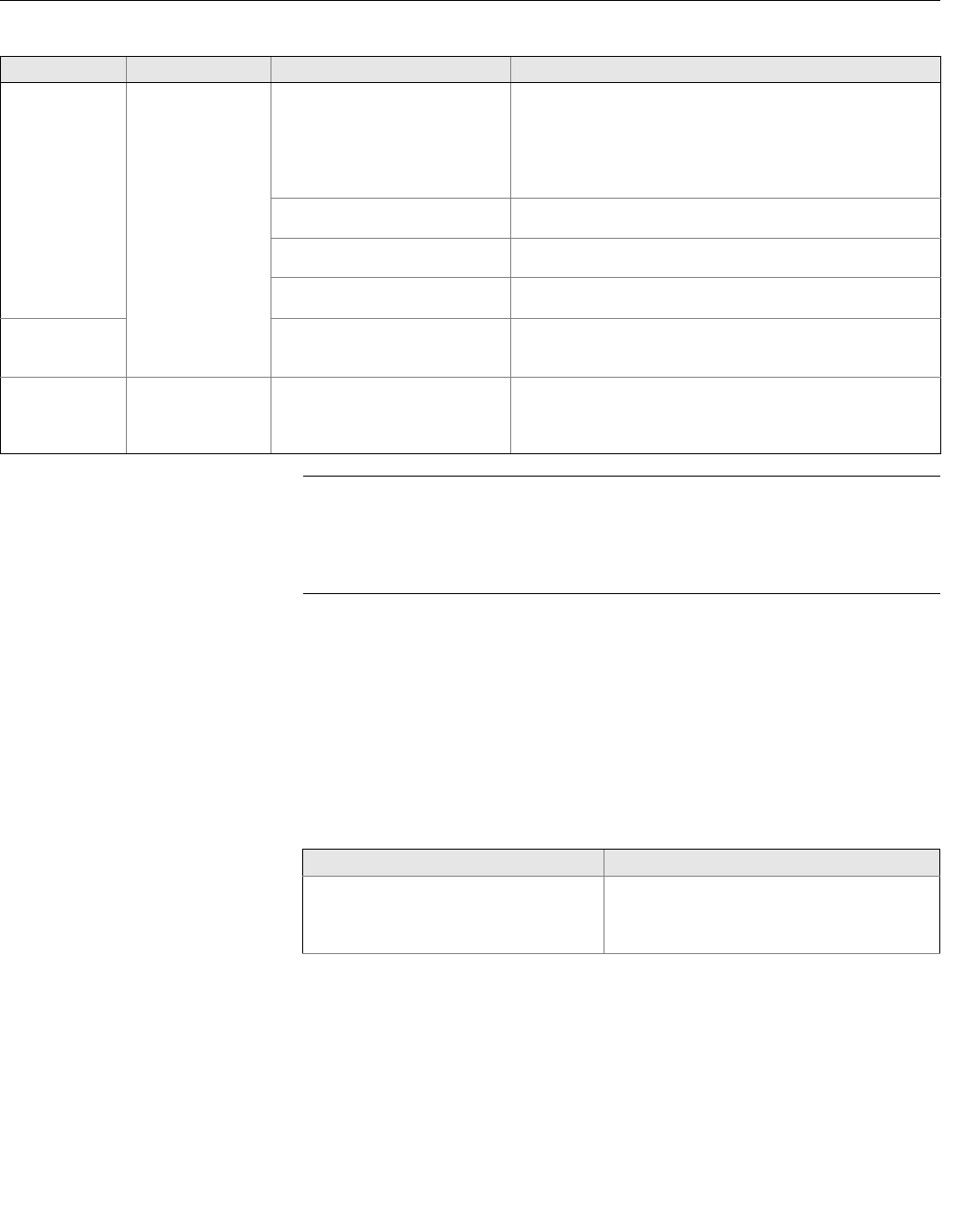
Reference Manual
00809-0100-4801, Rev FA
October 2010
7-19
Rosemount 3051S Series
NOTE
Rosemount cannot absolutely warrant or guarantee that Statistical Process
Monitoring will accurately detect each specific abnormal condition under all
circumstances. Standard maintenance procedures and safety precautions
should not be ignored because SPM diagnostic is enabled.
Troubleshooting the SPM
Diagnostic
Users are encouraged to pretest the SPM diagnostic if possible. For example,
if the diagnostic is to be used to detect plugged impulse lines, and if root
valves are present in the installation, the user should set up the diagnostic as
described earlier, and then alternately close the high and the low side root
valve to simulate a plugged impulse line. Using the SPM Status screen, the
user can then note the changes to the standard deviation or coefficient of
variation under the closed conditions and adjust the sensitivity values as
needed.
Low Variation
Detected / Low
CV Detected
LOW VARIA / LOW
CV
Plugged impulse line
(DP/AP/GP).
Follow facility procedure to check for and clear plugged
impulse lines. Both lines must be checked as the SPM
diagnostic cannot determine if the plug is on the high or low
side
(DP devices only). Conditions that lead to plugging on one side
may lead to an eventual plug on the other side.
Aeration decrease. If decrease is normal, reset and relearn. If not, check process
and equipment for change in operating conditions.
Decrease of liquid content in gas
or steam flow.
If decrease is normal, reset and relearn. If not, check process
and equipment for change in operating conditions.
Decrease in solids content. If decrease is normal, reset and relearn. If not, check process
and equipment for change in operating conditions.
Reduction in variability in process. If decrease is normal, reset and relearn. If not, check process
and equipment for change in operating conditions. For
example, a stuck control valve can reduce variability.
Mean Change
Detected
MEAN CHANGE Significant process setpoint
change.
If change is normal, reset and relearn. Consider changing
mean change detection to automatically relearn. If change is
not expected, check process and equipment for change in
operating conditions.
Table 7-6. Possible causes of SPM diagnostic events
Detection Type LCD Display Potential Cause Corrective Action
Table 7-7. Possible SPM issues and resolutions
SPM Diagnostic Issue Action
SPM diagnostic status indicates insufficient
variability and will not leave learning or
verifying mode
Process has very low noise. Turn off insufficient
variability check (Verification Criteria screen).
SPM diagnostic will be unable to detect a
significant decrease in noise level.