Manual
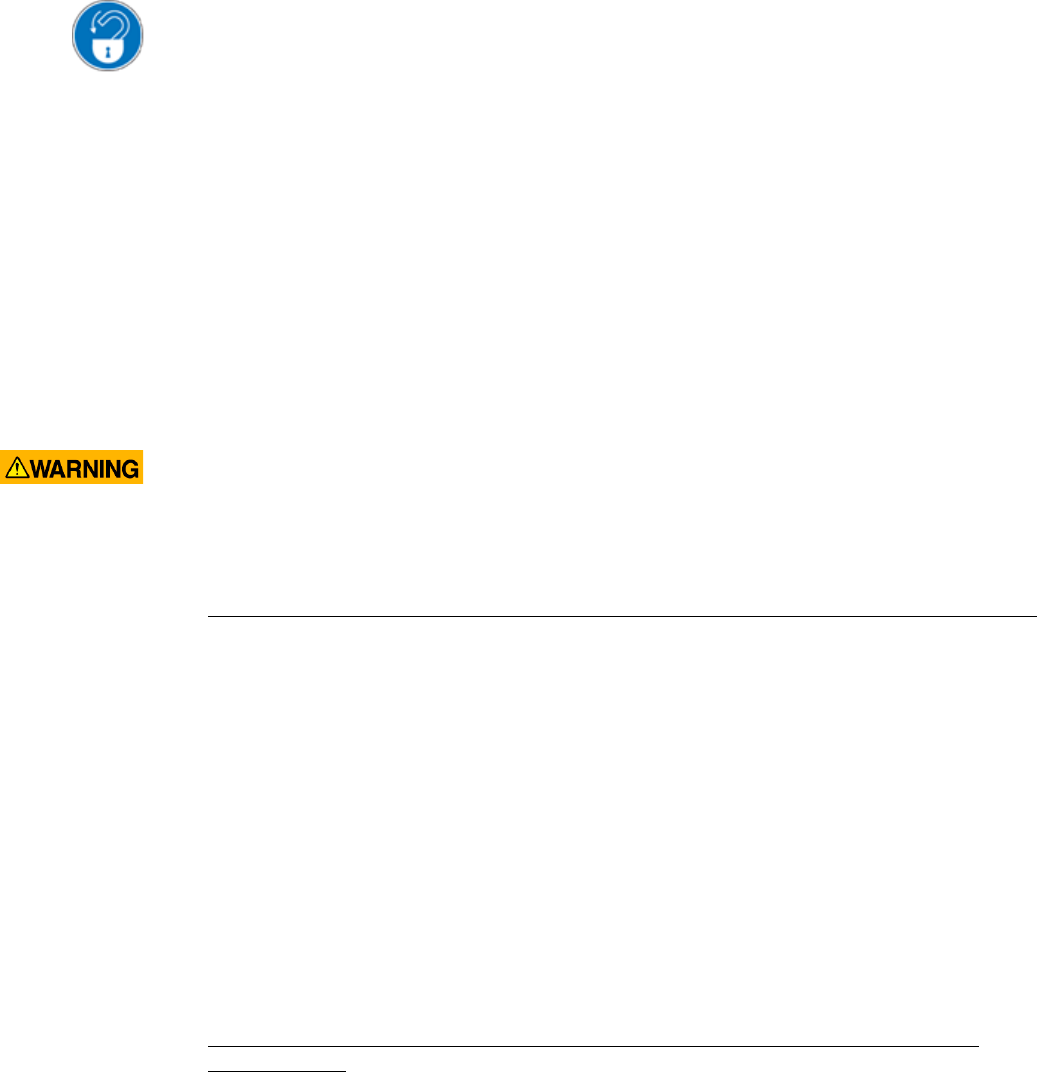
1000 Series Granulators Chapter 1: Safety 12 of 45
! ALWAYS DISCONNECT AND LOCKOUT the main electrical power to the
granulator before performing any service.
! SAFETY INTERLOCKS MUST NOT BE BYPASSED. The mechanical and
electrical safety interlocks ensure the safety of personnel. They should never be
tampered with or removed for ANY reason. They should be checked frequently by a
qualified mechanic for proper operation.
! NEVER modify the machine configuration or any individual component without
written notice from the factory.
For further information on granulator safety, installation and operation, see the American
National Standard for Plastics Machinery
!
Granulators, Pelletizers, and Dicers Used for
Size Reduction of Plastics
!
Construction, Care, and Use. ANSI B151.11-1982.
We have long recognized the importance of safety and have designed and manufactured our
equipment with operator safety as a prime consideration. We expect you, as a user, to abide
by the foregoing recommendations in order to make operator safety a reality.
Additional Warning:
The process of granulating and conveying materials inevitably creates dust levels that could
potentially cause a hazard if certain procedures or precautions are not followed. Hazardous
dust is defined as any material particle 420 microns or smaller (less than 40 mesh or .0164”)
which is dispersed in air or collected on surfaces more than 1/32” thick.
The following are some precautions that should be followed to avoid any dust related hazards.
1. Always use the largest granulator screen or regrind particle size for your process. The
larger the screen size, the less dust will be generated.
2. Know the specifics of the material you are granulating. If your material is especially
dusty, inquire about other equipment that may help in controlling the dust levels.
3. Keep the area around the granulator clean by minimizing leaks from the machine or
conveying/collection system. It is suggested that an industrial vacuum be used as needed
to keep the area clean.
4. When cleaning the granulator for color or material changes, an industrial vacuum is
recommended. Do not use compressed air to blow off material on machine surfaces.
5. Establish frequent knife gap maintenance procedures. Different materials have different
effects on knife wear and ultimately the operating knife gap. Large knife gaps (2 or 3
times the original setting) can generate higher dust levels.
Also note that the granulating process can generate heat sufficient to melt materials and
potentially cause fires or explosions.
The following are some precautions that should be followed to avoid any fire/explosion
related hazards.
1. Feed process materials at the appropriate rate consistent with the granulator throughput
capacity and screen size used for your material. Overfeeding can cause jam ups and/or
melting of process material which can outgas potentially explosive gas.
2. Monitor pneumatic conveying systems used to convey granulate from the granulator.
Loss of conveying can cause a material back up and ultimate melting and gas offing.
3. Maintain proper knife gaps on the granulator. Small knife gaps can result in knife
collisions which can then cause excessive friction, which heats the process material, and
may cause potential ignition.